Louis Armstrong International Airport
A visionary project of the City of New Orleans, the new terminal at Louis Armstrong New Orleans International Airport embodies the vibrant spirit and distinct culture of the Big Easy. The $1 billion project is one of the most visible symbols of infrastructure modernization in the Gulf South region post Hurricane Katrina.
According to the design team, the terminal’s architectural form evokes the geography of the Delta region and the soft curves of the Mississippi River. The curved, T-shaped building forms a gentle arc on three sides, and a monumental roof rises toward the structure’s centerline where it crests over a large central skylight. Designed to allow long spans, the spherical-shaped roof is supported by majestic concrete columns to reflect the region’s modern and upward trajectory.
Agileflow™, an Amrize Brand, was used to produce 350 majestic support columns.
The concrete needed to produce a smooth, high-end surface aesthetic with every pour.
The airport's high drop heights required an advanced SCC mix that flowed at higher capacities.
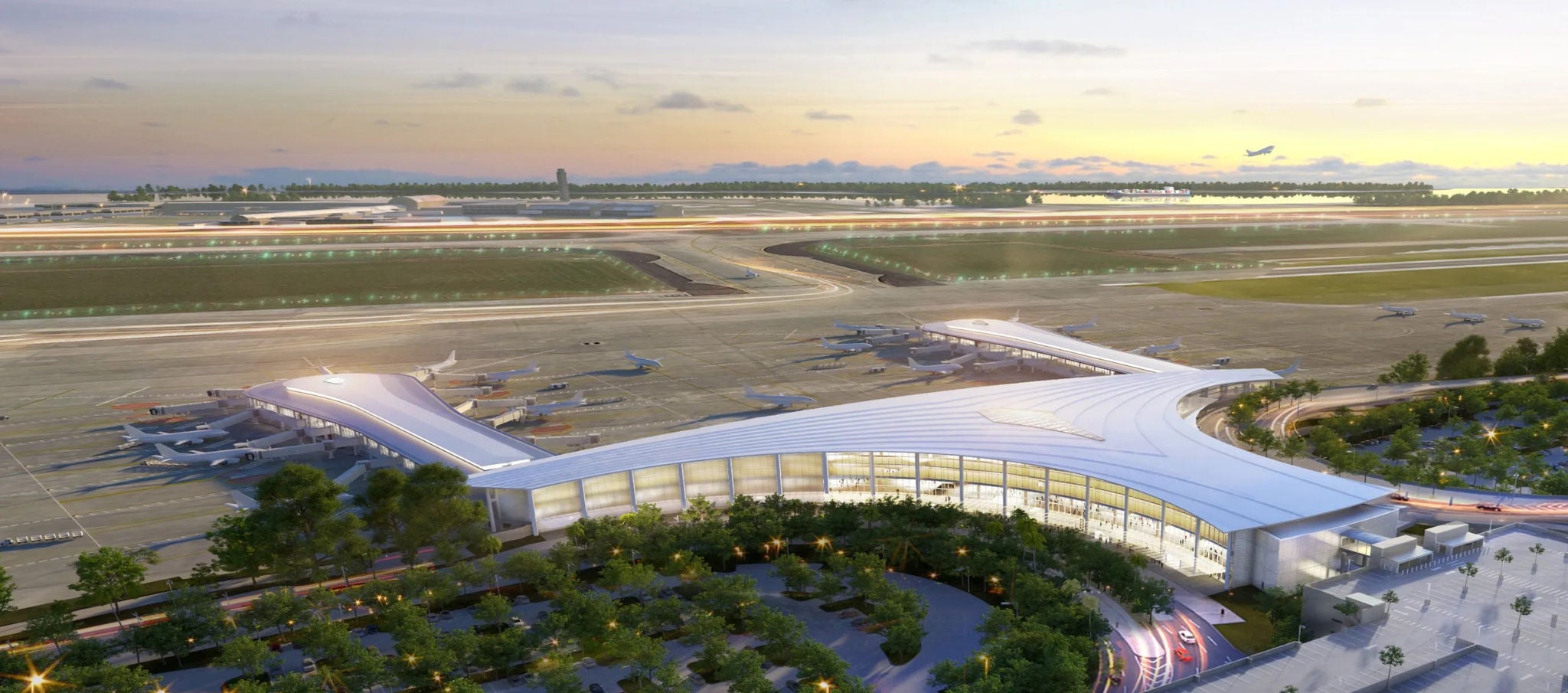
Our Ambition
To ensure its continued success as a primary commercial hub and destination for commerce, Louis Armstrong International Airport needed to expand its transportation and logistics infrastructure to accommodate for exponential growth in traffic and cargo volumes. Conceived by Pelli Clarke Pelli, the world-class design of the 972,000-square-foot replacement terminal features three concourses with 35 passenger gates, seamless connections between concourses, nearly 80,000 square feet of retail space, parking garages and a surface parking lot, and a spectacular concrete apron that ties into existing runways.
One of the biggest challenges in constructing the tall and complex columns was finding the ideal concrete mix that would perform on a variety of levels. The use of a conventional concrete was not an option for this application due to all the highly congested steel reinforcement, embeds and anchor bolts within the columns. In addition, project specifications required a high-quality class-A exposed concrete finish, which would not be possible using a standard concrete mix.
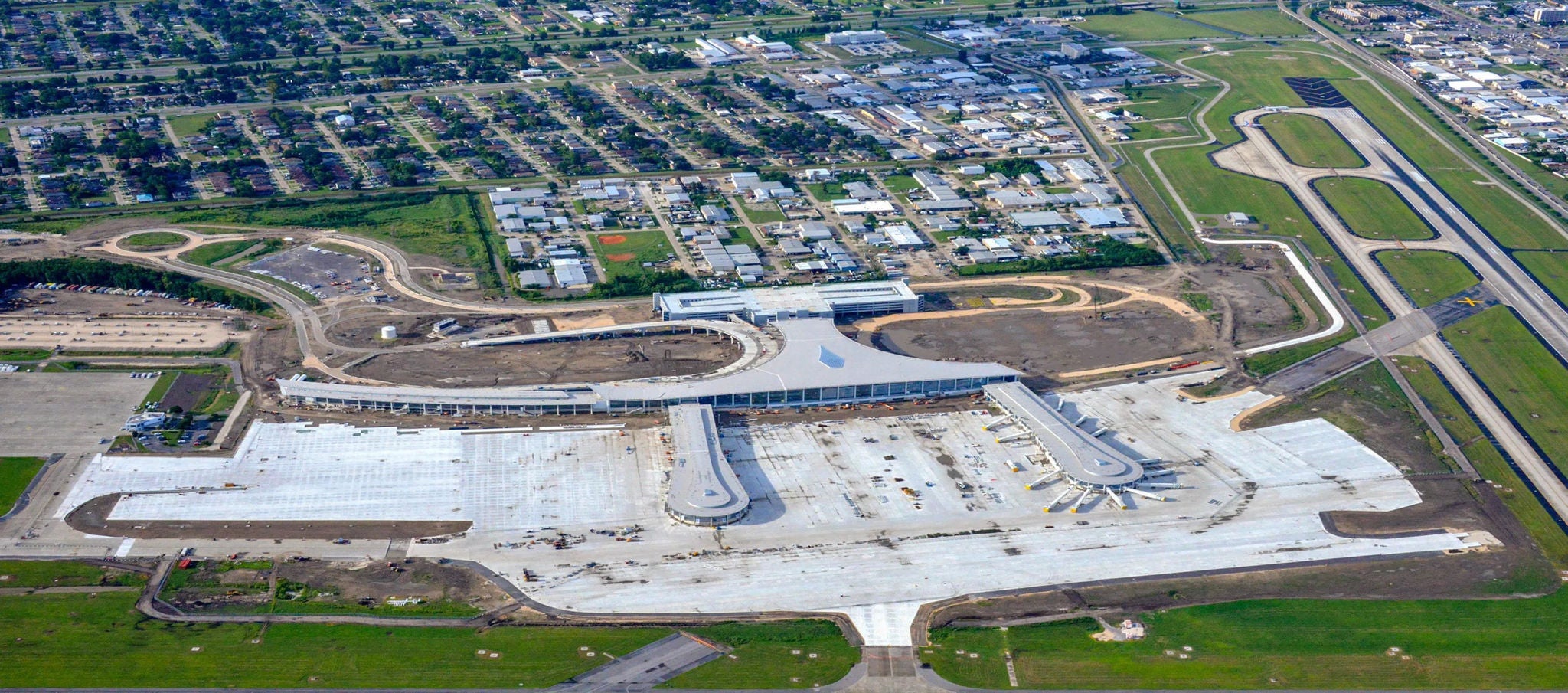
The Solution
To meet the stringent performance criteria for this high-vertical application, the project team selected Agileflow™ as the trusted building solution, helping to achieve the project’s most ambitious goals. This highly fluid concrete places more quickly than standard concrete, flows easily through highly congested reinforcement, and provides superior non-segregation properties for greater structural integrity. Other advantages of the SCC technology include increased strength, higher-quality finished surfaces and reduced production times and labor costs.
Primary considerations in developing the optimal concrete for the airport columns were flowability, viscosity, compressive strength, durability, and maximum temperature gain control. Key performance parameters included a compressive strength of 7,000 psi at 28 days, a maximum temperature of 95°F, and a spread of 28 to 31 inches.
“We design our Agileflow™ advanced SCC mixes to flow at higher capacities and to avoid separation in applications with high drop heights,” said BJ Eckholdt, quality control manager at Amrize. “With the concrete developed for the airport columns, we could easily take the spread to 31 inches, whereas most standard SCC mixes would fall apart at that mark.” To achieve specified performance goals, the SCC mix for the columns was formulated to control heat gain.
The Results
The new airport terminal is not only an example of outstanding design and stellar engineering but also a tribute to all the construction trades for making the architectural vision a reality.
Construction of the 350 structural columns took about 12 months and required more than 6,500 cubic yards of the Agileflow concrete to complete. The specified compressive strength on this project was 7,000 psi at 28 days; however, the SCC mix consistently achieved strengths surpassing 11,000 psi. The tailored mix with its self-consolidating properties was a great solution to column production challenges, and the surface finish allowed for the final field finish with minimal rubbing and patching — a huge benefit in terms of time and labor cost savings.
Our Brands at work for you
- Agileflow™